Préparation efficace des moules d'injection
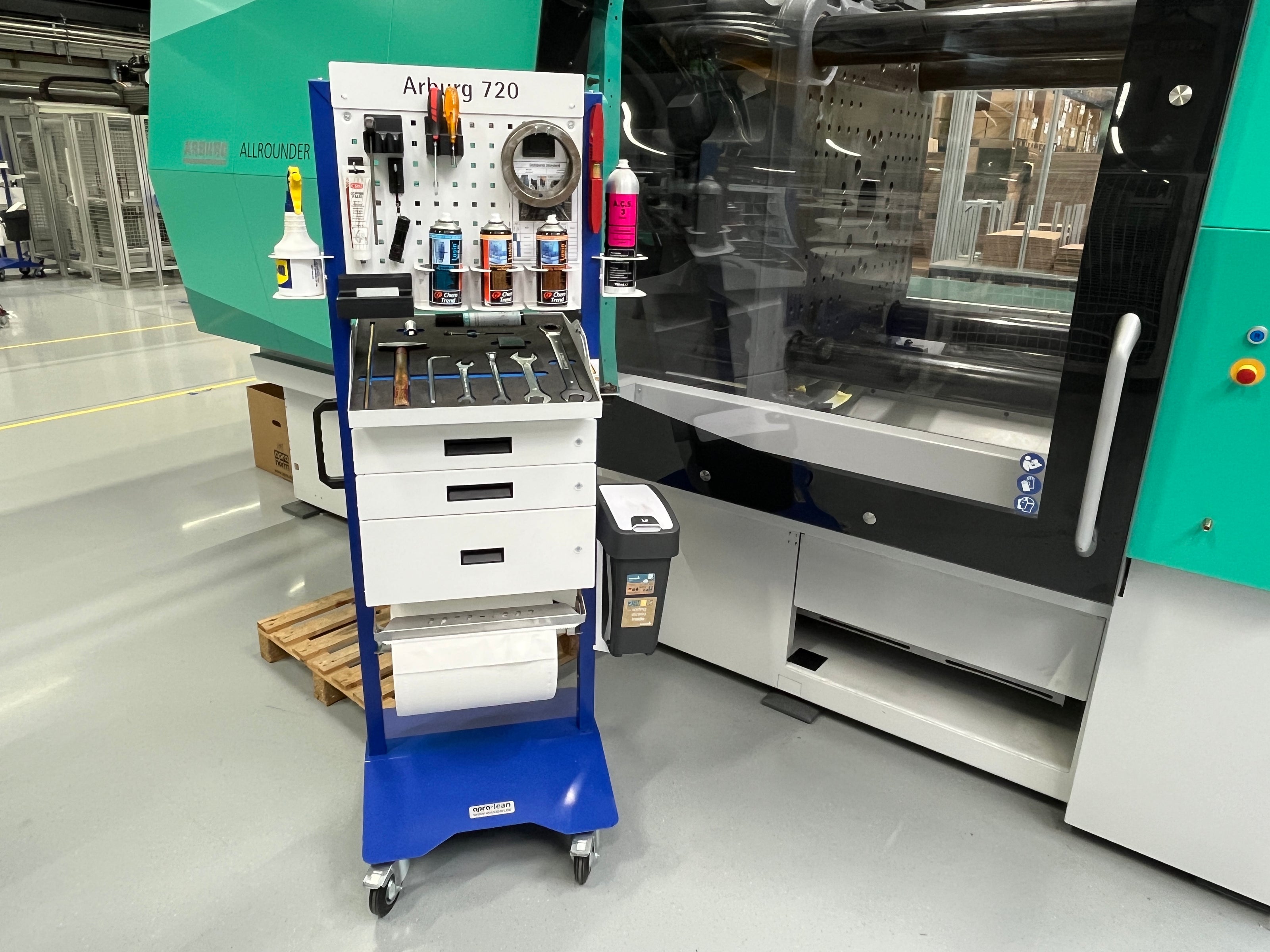
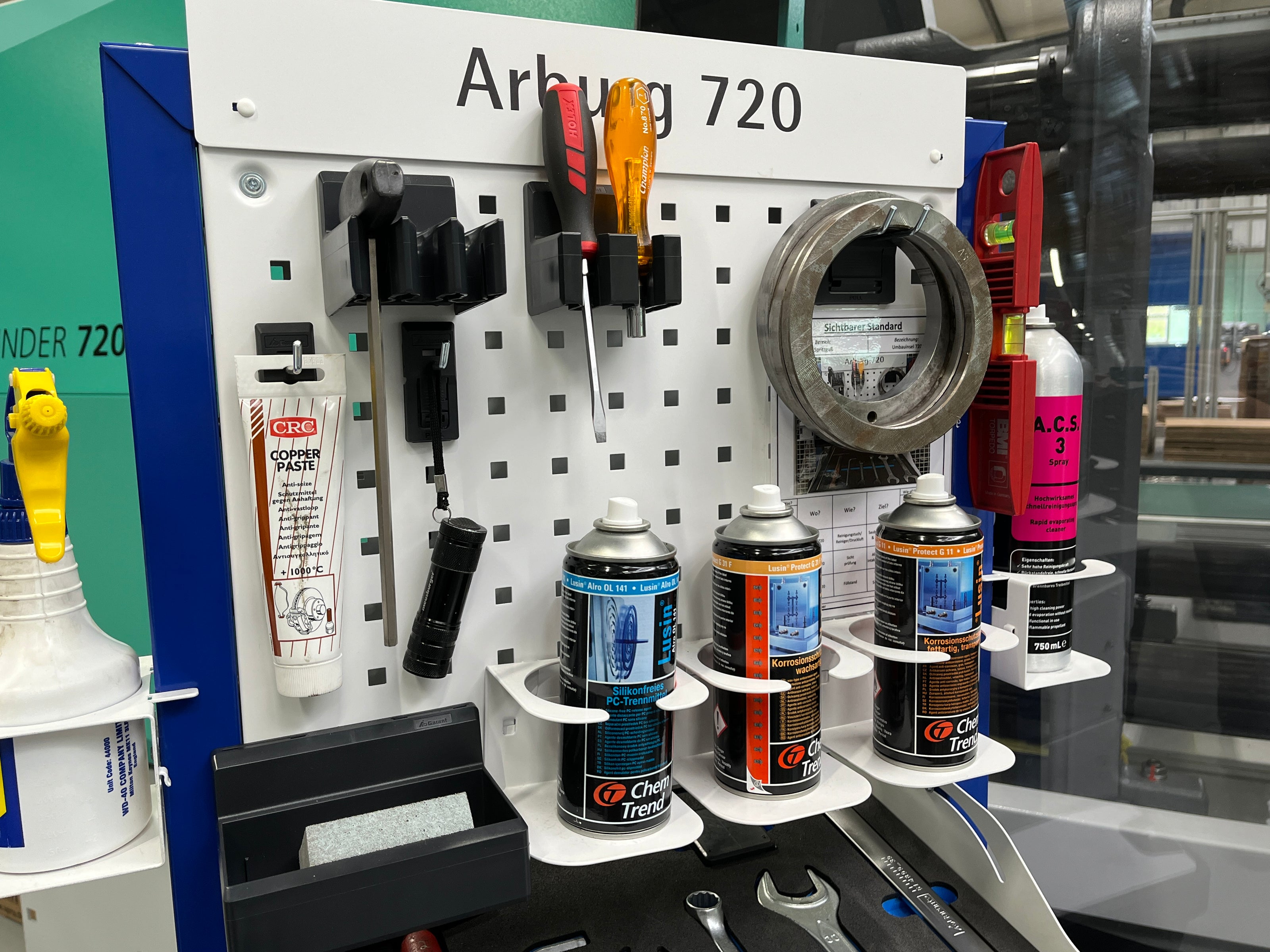

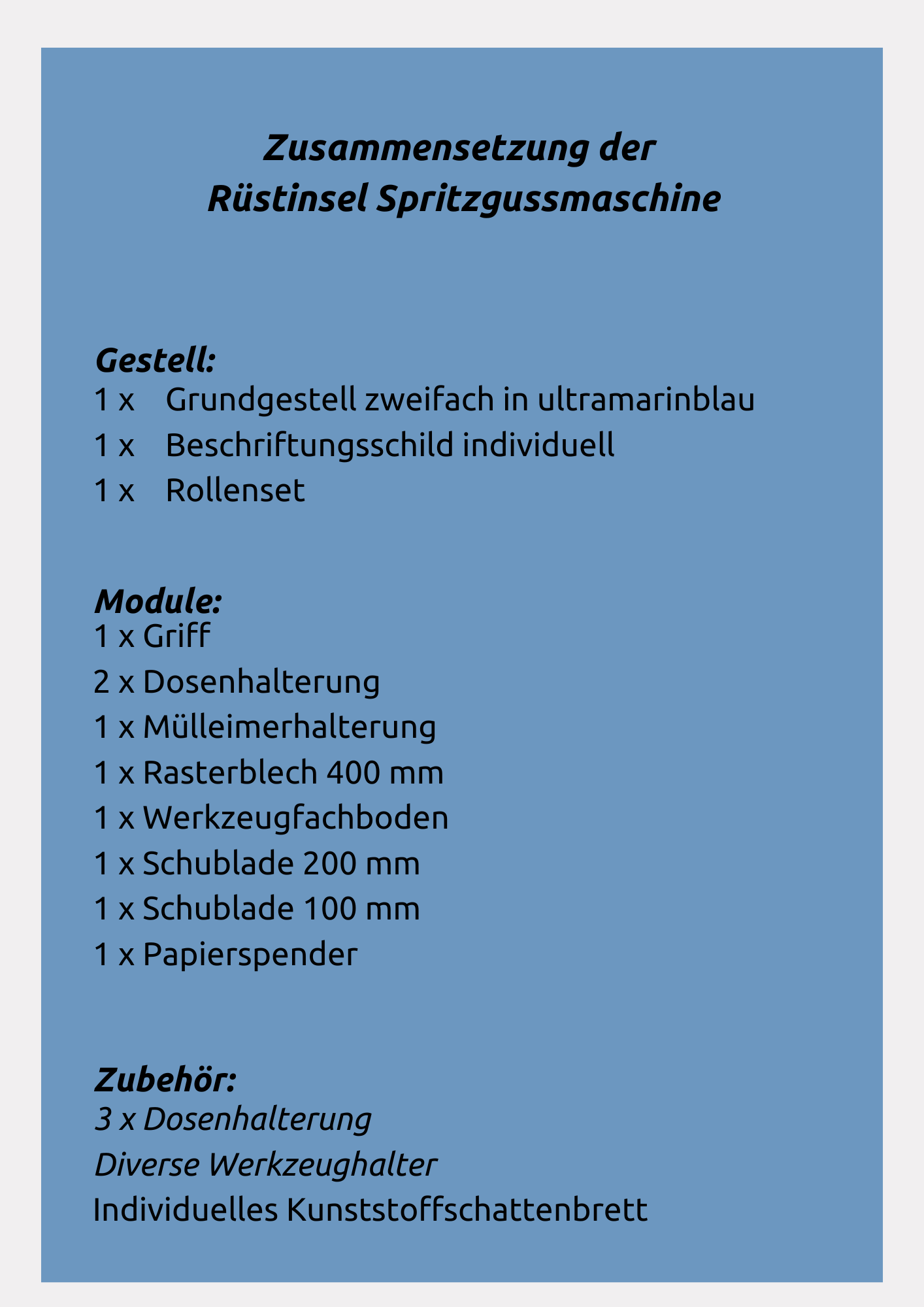
Dans la production de moulage par injection, les longs temps de préparation et les processus de travail désorganisés sont des problèmes fréquents qui entraînent non seulement des pertes d'efficacité, mais aussi des coûts inutiles. Dans cet article, nous vous montrons, à l'aide d'un exemple concret, comment il est possible d'obtenir des résultats impressionnants grâce à une optimisation ciblée des processus avec l'analyse SMED et la méthode 5S.
N'hésitez pas à prendre contact avec nous :
Le défi : minimiser les temps de préparation et de recherche
La production de moulage par injection de notre client était confrontée aux défis suivants :
- Longs temps de préparation : Les processus de changement prenaient beaucoup plus de temps que nécessaire.
- Surplus d'outils inutiles : Des outils trop nombreux ou défectueux rendaient la vue d'ensemble difficile.
- Frais de recherche élevés : Les outils étaient répartis dans des tiroirs et difficiles à trouver.
- Pas de normes : Des chariots à outils et des équipements différents ont entraîné des méthodes de travail incohérentes.
Ces problèmes ont entraîné non seulement des retards de production, mais aussi la frustration des employés.
La solution : un véhicule de préparation standardisé
En appliquant la SMED-Analyse (Single-Minute Exchange of Die) et le La méthode des 5S la préparation a été systématiquement optimisée :
- Analyse du processus de travail : Tout d'abord, les temps de préparation ont été analysés et tous les outils nécessaires ont été identifiés.
- Élimination du superflu : Les outils inutiles ou défectueux ont été systématiquement retirés.
- la standardisation : Un véhicule de préparation unifié a été développé et équipé de tous les outils pertinents.
- Ordre visuel : Chaque outil a été disposé de manière clairement visible afin d'éliminer les temps de recherche.
La clé de l'efficacité résidait dans un La clé de l'efficacité résidait dans un chariot de préparation apra-lean individuel, qui a été spécialement adapté aux besoins des employés.
Le bénéfice client : Plus d’efficacité dans le processus de préparation
Les avantages de cette optimisation parlent d’eux-mêmes :
- Temps de préparation réduits : Tous les outils sont à portée de main, ce qui accélère considérablement les changements.
- Méthode de travail standardisée : Chaque employé peut utiliser n'importe quel chariot de préparation efficacement, indépendamment de ses préférences personnelles.
- Clarté et visibilité : L’ordre visuel permet une identification immédiate et une mise en service rapide.
- Gestes plus rapides : L’ergonomie du chariot de préparation assure une utilisation intuitive et des processus plus fluides.
Conclusion : L’optimisation des processus en vaut la peine
Composition de Terminal de préparation en injection
-
Bâtis de base
Prix habituel À partir de €317,50 EURPrix habituelPrix unitaire / par -
Kit de roulettes
Prix habituel €79,65 EURPrix habituelPrix unitaire / par -
Panneau d’identification Impression individuelle
Prix habituel €79,65 EURPrix habituelPrix unitaire / par -
Tiroirs 2 x 100 mm
Prix habituel €252,50 EURPrix habituelPrix unitaire / par -
Tiroir de 200 mm
Prix habituel €190,00 EURPrix habituelPrix unitaire / par -
Distributeur de papier
Prix habituel €50,90 EURPrix habituelPrix unitaire / par -
Panneau perforé 400 mm
Prix habituel €82,75 EURPrix habituelPrix unitaire / par -
Étagère petit
Prix habituel €63,70 EURPrix habituelPrix unitaire / par -
Support de poubelle
Prix habituel €53,30 EURPrix habituelPrix unitaire / par -
Support pour boîtes / bouteilles
Prix habituel €25,30 EURPrix habituelPrix unitaire / par
1
/
de
11