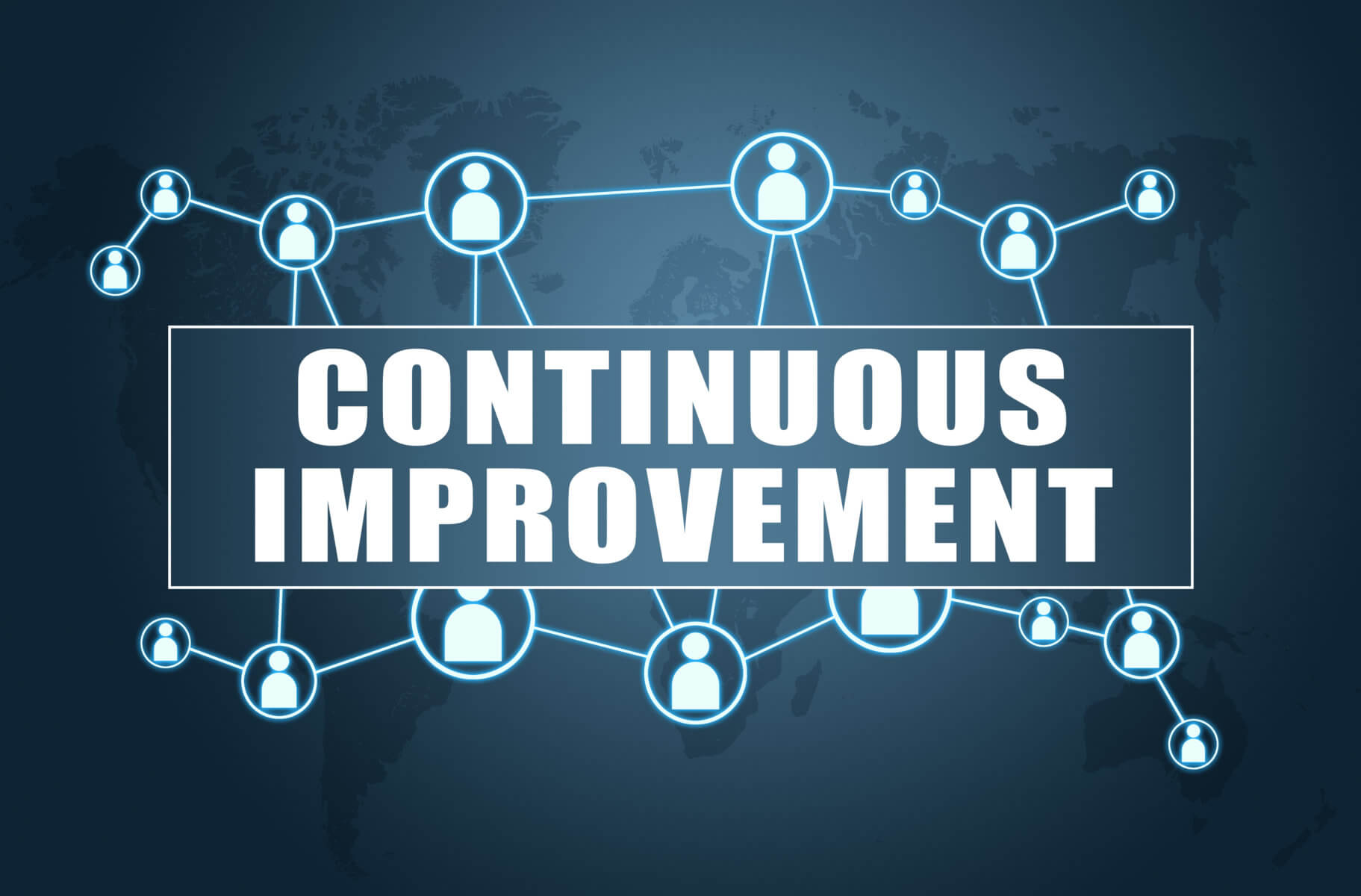
The Japanese word kaizen is made up of the words ‘kai’ (change, transformation) and ‘zen’ (for the better) and describes a method for the continuous improvement of activities, processes, procedures or products by all employees of a company. The kaizen principle can therefore be categorised as lean management.
Difference between the kaizen principle and BPR
In comparison to business process reengineering (BPR), which aims to implement radical changes in a short space of time, the kaizen principle describes continuous improvement in small steps involving all employees. In contrast, the focus of the Kaizen principle is on continuous quality improvement and cost reduction and is therefore seen as an integral part of quality management.
What goals can be achieved with the Kaizen principle?
All measures of the Kaizen principle are essentially aimed at increasing customer satisfaction. This is to be achieved through three factors:
- cost reduction,
- quality assurance,
- speed (time efficiency)
It is important that all employees and company departments are involved. This is the only way that improvements in line with the Kaizen principle can be effective across all levels.
The 5 pillars of the Kaizen principle
The Kaizen principle is based on these five basic principles, which set the continuous improvement process (CIP) in motion.
Process orientation
Instead of focussing solely on the result, the Kaizen principle focuses primarily on the entire process. This is documented and analysed in order to continuously optimise the process standard and ultimately maximise profits in this way.
Customer orientation
The kaizen principle distinguishes between external and internal customers. Internal customers include, for example, other departments involved in the manufacture of the product. If defects are identified in the product during further processing, for example, this is reported back in order to avoid subsequent defects. In order to maximise customer satisfaction, transparent and trouble-free communication at these interfaces is essential.
Quality orientation
Quality assurance and improvement is of great importance in the Kaizen principle. Elaborate measurement procedures, permanent controls and defined key figures are intended to keep quality at a consistently high level.
Criticism orientation
The Kaizen principle expressly welcomes criticism! This is because such feedback serves the purpose of continuous improvement. Every employee can and should make suggestions, which are constructively taken on board by management and used accordingly.
Standardisation
Improvements that have been implemented and have proven themselves are introduced as standard. Only once such a standard has been established is further improvement sought.
Which methods is the Kaizen principle based on?
We provide an overview of the most important methods within the Kaizen principle:
5S
The 5S are a method from lean management and a fundamental method of the Kaizen principle. The 5S consist of these five consecutive steps:
- Sort (Seiri)
- Set in order (Seiton)
- Shine (Seiso)
- Standardize (Seiketsu)
- Sustain(Shitsuke)
We explain more about this in our post 5S method.
The 7 Muda
The 7 Muda identify seven types of waste that are considered typical sources of loss. These are in detail:
- Muda due to overproduction
- Muda due to waiting time
- Muda due to unnecessary transport
- Muda due to the production of faulty parts
- Muda due to excessive storage
- Muda due to unnecessary movement
- Muda due to an unfavourable manufacturing process
For more information, read our article The seven muda.
The 7M checklist
The 7M checklist contains the most important factors that need to be regularly scrutinised:
- People
- Machine
- Material
- Method
- Environment/Co-environment
- Management
- Measurability
Our products
-
5S Cleaning and Hygiene
Cleaning stations for production, workshops and officesThe apra-lean cleaning stations offer an...
-
5S Production / 5S Assembly
Process stations for production and assemblyThe apra-lean process stations are compact and...
-
Shopfloor Management and Workshop
The shop floor station is a mobile information board for use in...
-
First aid and Safety
Safety and a quick response option in the event of emergencies in...
-
Customised solutions
Wir entwickeln gemeinsam die perfekte Lösung für Ihre Anforderungen!