
Workplace organization as a success factor
Imagine: As a skilled worker, you enter a production hall and find an orderly, modern work environment. A clearly structured workplace, tidy materials and efficiently designed processes signal that this company places value on quality and professionalism. In times of a shortage of skilled workers, a modern work environment is becoming increasingly important for companies in order to attract and retain motivated employees. A successful lean production strategy, supported by the 5S method, creates precisely these conditions and promotes a committed and satisfied workforce.
Why workplace organization determines success and motivation
Productivity, efficiency and employee satisfaction are closely linked. A workplace that is carefully designed and responds to the needs of skilled workers ensures a professional work environment and reduces frustration factors such as long search times or inefficient processes. A clear structure is essential, particularly in production environments where several employees work together at one workstation.
The challenge of outdated systems
In many companies, "historical systems" are passed on from one generation to the next, often without critical examination. Outdated processes and inefficient structures disrupt the workflow, lead to dissatisfaction and pose potential safety risks. In order to motivate specialists and successfully implement Lean Production, companies must have the courage to question and optimize existing systems.
Small changes with a big impact: The 5S method
A proven method for improving workplace organization is the 5S method. This concept from Japan helps companies to create clear structures and maintain them permanently. The five steps of the 5S method provide a simple but effective framework for a motivating workplace culture:
- Select – Remove unnecessary material and make room for the essentials.
- Systematize – Arrange tools and materials so that they are quickly accessible.
- Clean – Ensure that workplaces are clean and regularly maintained.
- Standardize – Define uniform specifications to increase flexibility and efficiency.
- Self-discipline – Long-term compliance with standards, even on stressful working days.
By consistently implementing these steps, the workplace becomes a source of motivation for skilled workers. Efficiency, safety and flexibility promote a pleasant working atmosphere and reduce unnecessary frustration.
The advantages of lean production for skilled workers and companies
Successful lean production has a positive effect on the entire company and motivates skilled workers:
- Efficiency and flexibility: Fixed places for each tool and standardized processes shorten search times and improve work quality.
- Safety: A tidy workplace minimizes the risk of accidents and improves work safety.
- Quality and cost savings: Less tool loss and material waste reduce costs and increase product quality.
Lean production promotes a productive and pleasant working environment that pays off for both employees and the company.
Managers as role models for lean production
Implementing changes requires perseverance and persuasiveness, especially with long-term employees. Managers play a central role here: They set a good example and actively involve their employees in the design of the workplace. Young specialists in particular often embrace new ideas with enthusiasm and can act as multipliers for the 5S method.
Conclusion: Motivate specialists with Lean Production
With Lean Production, companies create the conditions for a modern, structured work culture. The 5S method helps to create a clean, safe and productive environment that motivates specialists and increases efficiency.
Take the first step towards a modern 5S workplace culture.
Find out more about our Lean Production solutions.
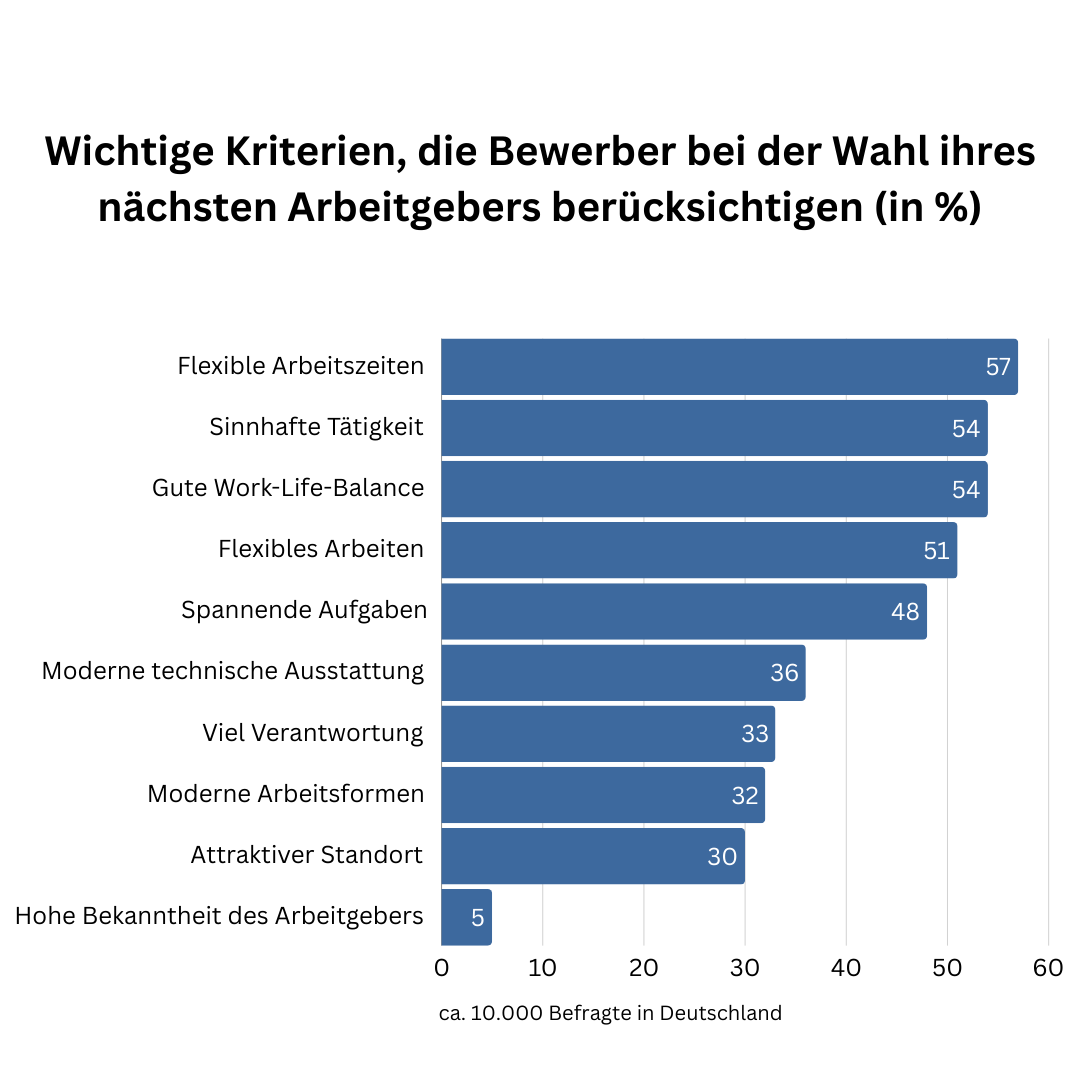