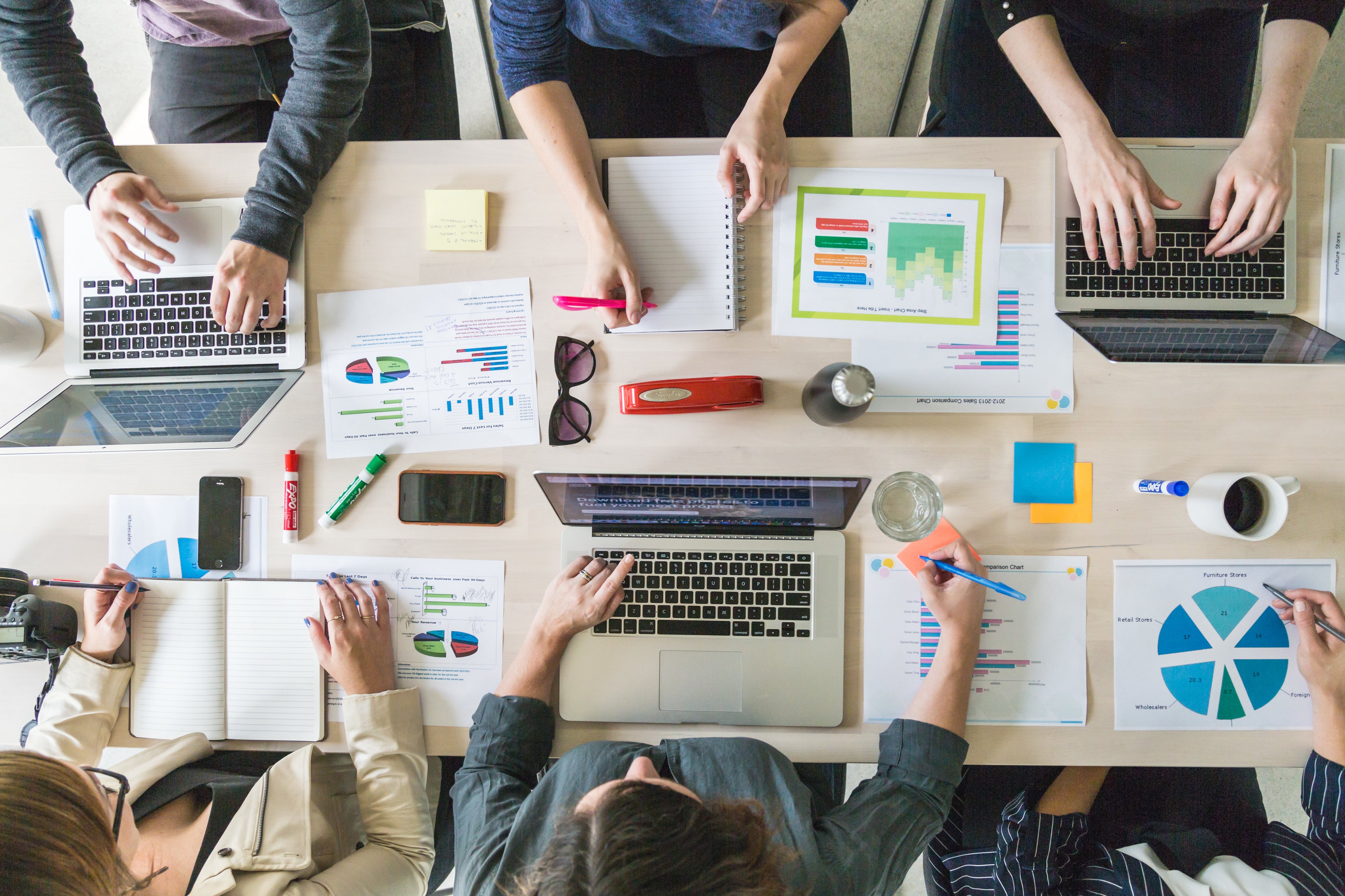
How Lean Management can improve your work processes
Constant change and global crises are making our everyday lives increasingly difficult and stressful, so it is essential to work on and rethink some entrenched structures. This raises the question: "Is the way we act still sensible and efficient enough to keep up with today's standards?" Whether as a private individual or in everyday working life, you are constantly confronted with the need to improve and optimize processes. Especially at work, with increasing staff and skilled labor shortages, it is important to revise existing structures and optimize work steps as a result, or even eliminate them. This article introduces the "Lean Production" method and explains the advantages of this method.
Definition and origin of Lean Production
What does "Lean Production" actually mean? The origin of Lean Management goes back to a special production system used by the Japanese car manufacturer Toyota. In the 1950s they increasingly had problems with a shortage of raw materials, limited financial resources and a lack of space. A solution had to be found so that the company could continue to exist in the future. The idea was to offer the highest quality in the shortest time possible and to generate optimal costs by identifying and eliminating waste and irregularities in the production processes. This approach gave rise to the Just-in-time principle. This principle includes the concept of only delivering and producing materials in the number and at the time required by customer orders. In a study in the 1990s, the authors referred to this production system as Lean Production
or in German, lean production. Analogous to this term, concepts such as Lean Administration and Lean Maintenance quickly emerged. The term Lean Management now combines all company processes - from administration to production - and considers the entire value chain. Due to today's market requirements in the industrial sector, Lean Production is more relevant than ever before. High competition and time pressure, increasing customer demands and cost sensitivity. Companies that want to remain competitive must align all production processes with demand and make them cost-efficient.
Goals of Lean Production
Lean production uses several processes to help reduce waste in companies and minimize costs through efficient use of resources. In general, processes are streamlined, as the term "lean" suggests. In production, processing times are shorter and more well thought out, which increases product variety and customer satisfaction through short delivery times.
The 5S method
Lean production is generally assigned to lean management, as is the 5S method. This method is a systematic approach to designing your own work environment. Its goal is to minimize waste and replace it with a structured organization of the workplace. Their origins are also in Japan. The five "S" are derived from the terms Seiri, Seiton, Seiso, Seiketsu and Shitsuke. Translated into English, it means the description of the steps of the 5S method : Sort, Set in order, Shine, Standardize and Sustain.
The 5 Lean Principles
Broadly speaking, there are 5 Lean Principles. The focus of the Lean principles is on optimizing processes in management. Efficiency and quality are ensured by coordinating customer needs. The aim of a continuous production process is to eliminate bottlenecks and only produce when the customer orders them in order to minimize storage costs. Employees should always be encouraged to question processes and make suggestions for optimization. This will increase efficiency in production in the long term.
Lean only works in a team
Introducing lean production into your company is basically makes sense if you are active in the area of mass production. You have the opportunity to reduce your costs by responding more efficiently and better to current market needs. You can make your processes more effective and thereby increase your competitiveness. The improvement in the quality of your products and productivity can be guaranteed, as revised work steps help to replace unnecessary processes with more efficient methods. Inventories, factory space and personnel are reduced to a minimum, which again leads to cost reduction. Manufacturing and ordering according to requirements and customer requests and wishes means that the intermediate storage associated with additional costs is eliminated and production surpluses can be avoided.
If you as a company decide to introduce lean production, then the first step will involve a number of work steps for everyone involved, because restructuring the original processes requires a lot of analytical thinking. Employees must be given the opportunity to get involved and make suggestions for improvement, because this change will basically make their everyday work easier. Measures can only lead to long-term success if everyone involved sees the point in the changes and the process is continued continuously. This shows once again how important it is to involve all employees and get them on board!
Lean production is not a sprint, but a continuous run
In general, it can be said that lean production has a positive effect on productivity, lead times, warehousing and process quality. However, it is important that all employees are involved and that there is a certain willingness to question and adapt existing processes and procedures. As already mentioned, there are a number of different approaches to implementing lean production in your company. Regardless of which lean concept you want to use, the motto applies: "This is not a sprint, but a continuous run."
Our products
-
5S Cleaning and Hygiene
Cleaning stations for production, workshops and officesThe apra-lean cleaning stations offer an...
-
5S Production / 5S Assembly
Process stations for production and assemblyThe apra-lean process stations are compact and...
-
Shopfloor Management and Workshop
The shop floor station is a mobile information board for use in...
-
First aid and Safety
Safety and a quick response option in the event of emergencies in...
-
Customised solutions
Wir entwickeln gemeinsam die perfekte Lösung für Ihre Anforderungen!