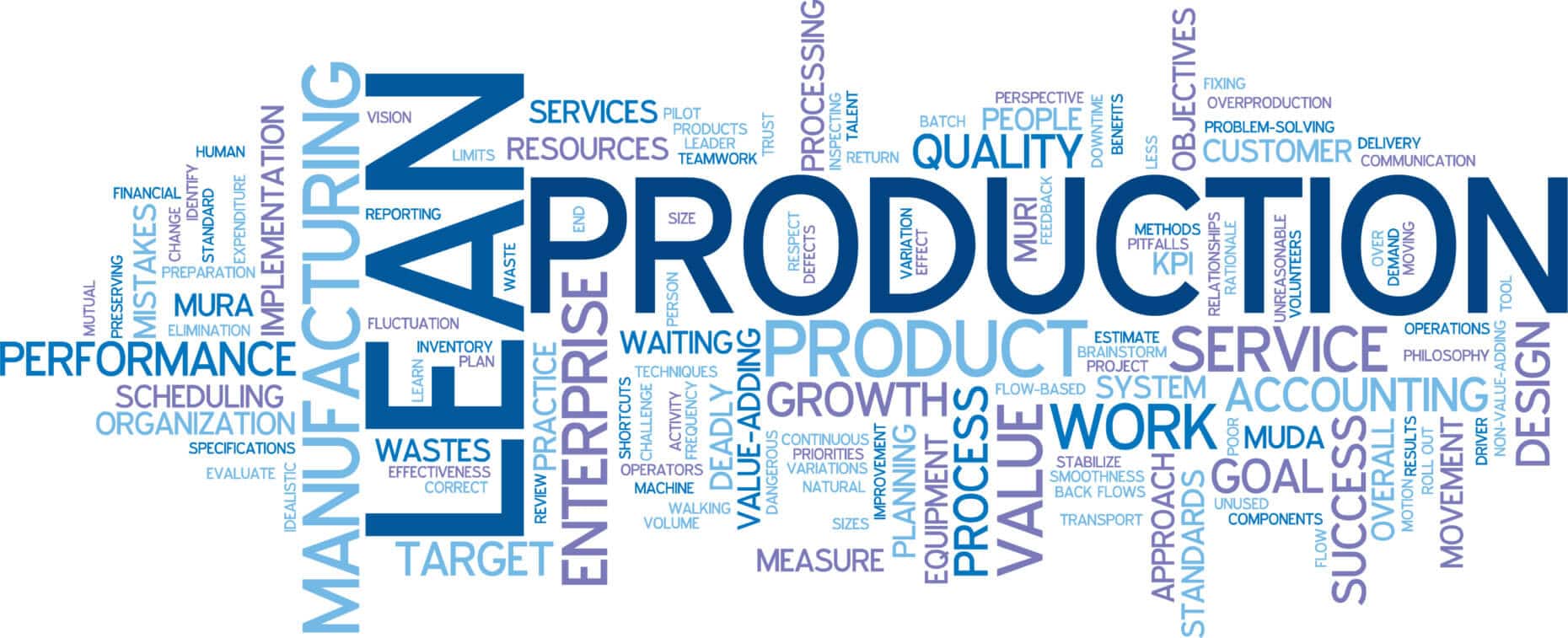
The ideas of lean principles and lean management were born in Japan after the Second World War with the guiding principle of making optimal use of the resources that were scarce at the time. In the early 1990s, the automotive industry began looking for ways to improve production quality and efficiency. Toyota in particular is considered a pioneer here. The principles of Lean management (also called Lean Thinking or, in an industrial environment, Lean Production) are intended to create value without wasting time, resources and materials. To do this, it is necessary to optimally coordinate the necessary activities and required materials.
This is what lies behind the 5 Lean principles
This article explains the 5 Lean management principles that form the guidelines for reviewing the existing system.
1. Define the value from the customer's perspective
The first of the Lean principles states that you should carefully examine what is to be produced and tailor the products precisely to the customer's needs. The customer should receive their individual product in the best possible quality at an adequate price, at the right time and in the right place.
2. Identify the value stream
The next of the Lean principles provides for a detailed examination of all the processes necessary for the creation of the services from the raw material to the customer. The value stream describes all the activities required to manufacture the product. All other, unnecessary activities must be eliminated from the process in order to avoid waste, optimize alignment with customer needs, and use all resources efficiently.
3. Implement the flow principle
The flow principle describes the design of production as a continuous and smooth process. Intermediate storage and buffer stocks lead to costs. The prerequisite for flexible, order-related and efficient control of production is the elimination of bottlenecks, the harmonization of production, and the alignment of this with the value stream.
4. Introduce the pull principle
The machines are not utilized according to maximum capacity; production only begins when the customer orders or stocks have reached a minimum. In the fourth of the five lean principles, also known as the pull principle, products are pulled through production from the customer's perspective instead of being pushed into production using planning specifications in order to achieve 100 percent delivery reliability. On the one hand, there is no need to store partial products and finished goods and the associated search and transport effort, and on the other hand, production can also be relieved of personnel.
5. Strive for perfection
The last step within the five lean principles describes the continuous pursuit of perfection, because according to the lean management idea, standing still means going backwards. The continuous improvement process (CIP) should continually encourage employees to question processes and contribute ideas in order not to fall back into old behavior and bad habits.
Our products
-
5S Cleaning and Hygiene
Cleaning stations for production, workshops and officesThe apra-lean cleaning stations offer an...
-
5S Production / 5S Assembly
Process stations for production and assemblyThe apra-lean process stations are compact and...
-
Shopfloor Management and Workshop
The shop floor station is a mobile information board for use in...
-
First aid and Safety
Safety and a quick response option in the event of emergencies in...
-
Customised solutions
Wir entwickeln gemeinsam die perfekte Lösung für Ihre Anforderungen!
1
/
of
5