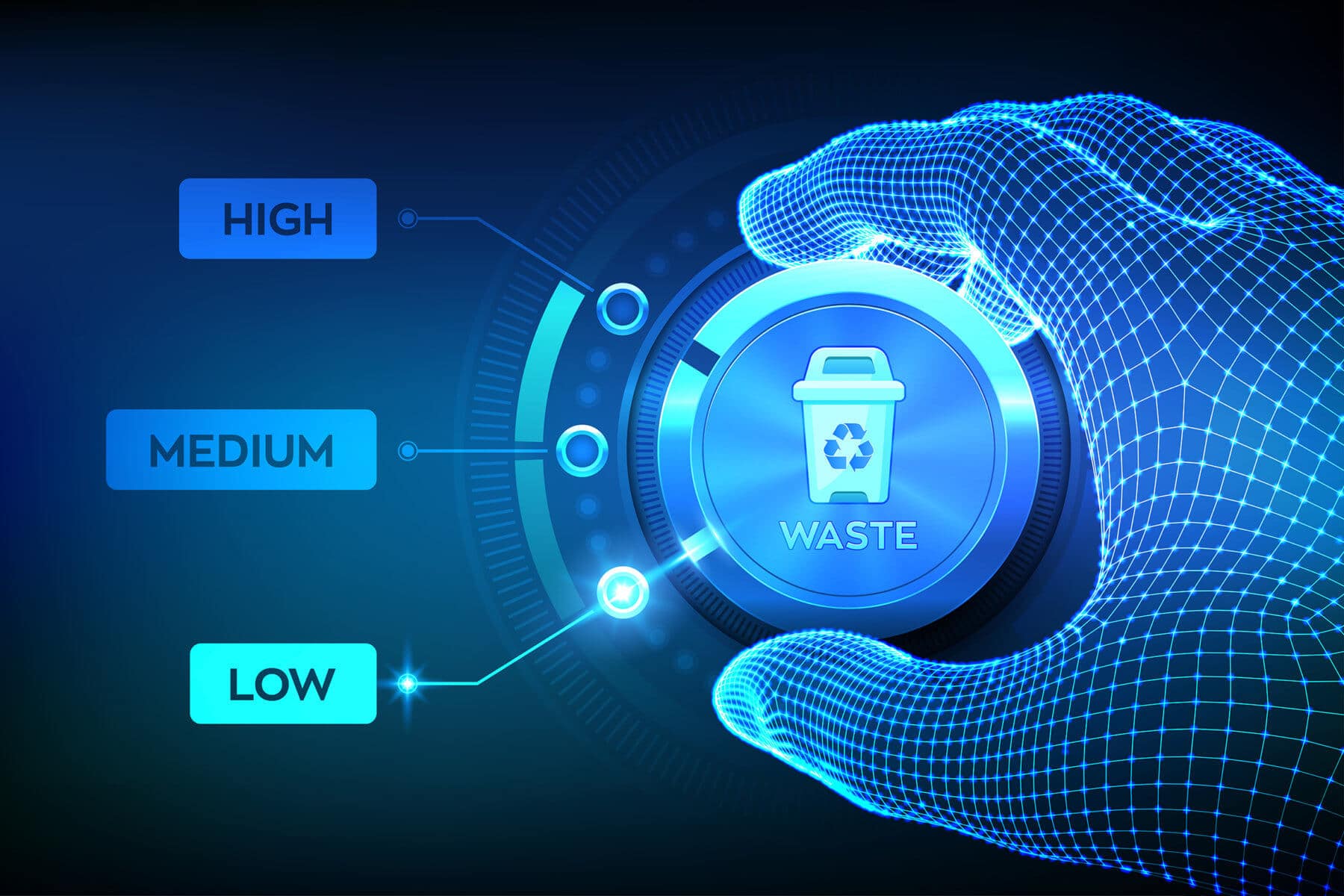
Waste, which is translated as ‘muda’ in Japanese, is repeatedly referred to in the context of lean management. Waste itself is often the cause of losses that can occur anywhere in the company, but also offers great potential for reduction.
The seven muda are:
- Waste due to overproduction: More is produced than is necessary.
- Waste due to waiting time: idle hands of an employee, poor process timing
- Waste due to excess transport: value-adding movement of materials or products
- Waste due to production of faulty parts: They disrupt the production flow and require expensive rework.
- Waste due to excessive storage: stockpiled inventory does not add value and causes storage and warehousing costs.
- Waste due to unnecessary movement: consumes time, leads to fatigue and increases the risk of injury
- Waste due to unfavourable manufacturing process: products are equipped with features that are neither needed, desired nor paid for by the customer.
The use of the acronym TIMWOOD is another way of identifying the types of waste.
T = avoid unnecessary Transport routes
I = avoid unnecessary inventory
M = avoid unnecessary movements (motion) avoid unnecessary movements (Motion)
W = avoid unnecessary Waiting times
O = avoid Over- Production
O = avoid unnecessary processes (Over-engineering)
D = avoid errors (Defects)
Waste can be minimised by analysing the causes of muda and applying lean management methods, costs can be saved and production processes optimised.
Our products
-
5S Cleaning and Hygiene
Cleaning stations for production, workshops and officesThe apra-lean cleaning stations offer an...
-
5S Production / 5S Assembly
Process stations for production and assemblyThe apra-lean process stations are compact and...
-
Shopfloor Management and Workshop
The shop floor station is a mobile information board for use in...
-
First aid and Safety
Safety and a quick response option in the event of emergencies in...
-
Customised solutions
Wir entwickeln gemeinsam die perfekte Lösung für Ihre Anforderungen!