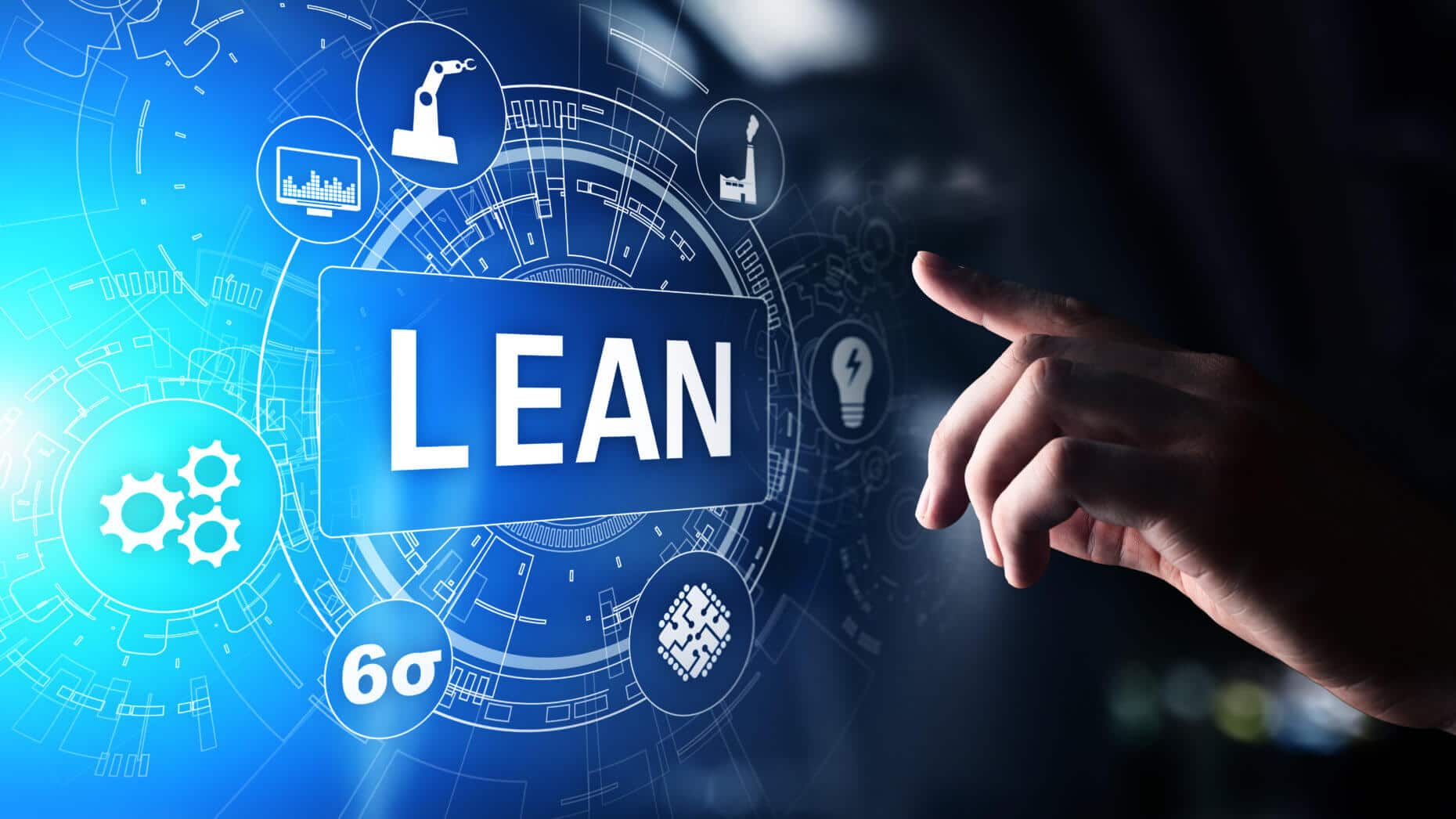
Lean management is an approach to process optimization in which waste is minimized and processes are harmonized. The term "lean management" originates from the English-speaking world and can be translated into German as "slim management". This method has its origins in the Toyota production system, which focuses on creating stable process organizations. These form the basis of the quality level achieved by Toyata products.
The aim of lean management is to avoid any form of waste, errors and unnecessary costs in all areas of the company and at the same time achieve the best possible quality. All activities that are necessary for value creation should be optimally coordinated and superfluous activities eliminated. To do this, both the customer perspective must be considered in order to be able to implement customer wishes for availability, individuality, quality and pricing, as well as the view of the company, which must function profitably and improve competitiveness.
By implementing process definitions, interface descriptions, clear responsibility structures, early reactions to errors and simple organizational methods, stable processes with a high level of customer orientation are created.
10 principles of lean management
In the literature according to Graf-Götz and Glatz, there are 10 design approaches for implementing lean management
- Orientation of all activities towards the customer (customer orientation)
- Concentration on your own strengths
- Optimization of business processes
- Constant improvement of quality (continuous improvement process, CIP)
- Internal customer orientation as a corporate mission statement
- Personal responsibility, empowerment and teamwork
- Decentralized, customer-oriented Structures
- Leadership is service to employees
- Open information and feedback processes
- Attitude and cultural change in the company (Kaikaku).
Our products
-
5S Cleaning and Hygiene
Cleaning stations for production, workshops and officesThe apra-lean cleaning stations offer an...
-
5S Production / 5S Assembly
Process stations for production and assemblyThe apra-lean process stations are compact and...
-
Shopfloor Management and Workshop
The shop floor station is a mobile information board for use in...
-
First aid and Safety
Safety and a quick response option in the event of emergencies in...
-
Customised solutions
Wir entwickeln gemeinsam die perfekte Lösung für Ihre Anforderungen!