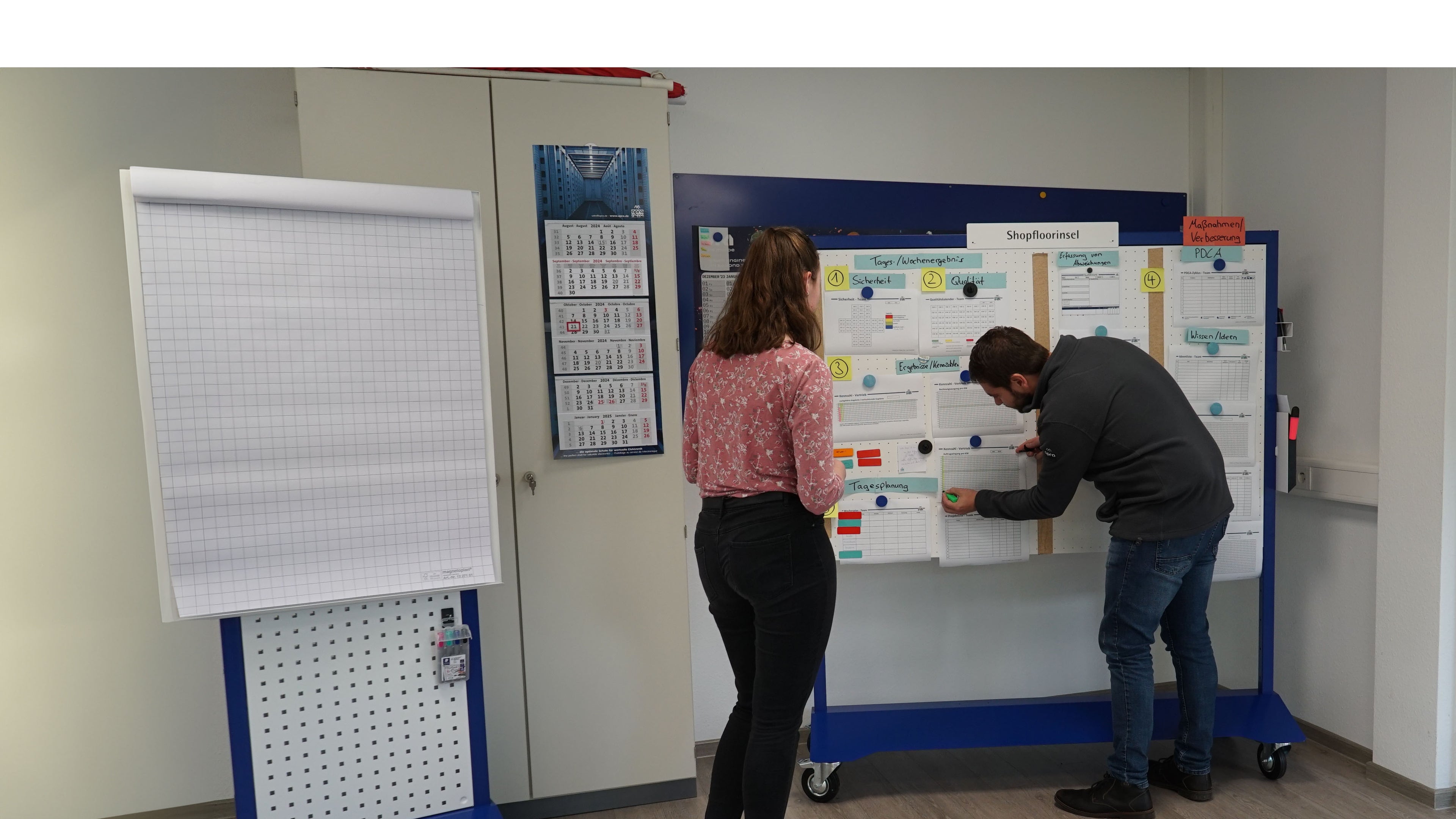
The term shop floor management refers to a management method that aims to manage the production area efficiently and effectively. It is important that employees work together so that problems can be identified quickly and a solution can be found to implement continuous improvements.
Implementation of shop floor management:
The implementation of shop floor management begins with the creation of a clear structure in which goals and responsibilities are initially defined. The managers determine which improvements are to be achieved through shop floor management.
A central component of shop floor management are regular shop floor meetings, which usually take place daily or weekly. In these meetings, current topics are discussed, e.g. a review of the previous day, the current production figures and quality values, as well as specific challenges. Causes of problems are sought together and measures for improvement are defined. These meetings also ensure that employees are actively involved in decision-making processes, which increases their personal responsibility. Through close cooperation, knowledge and skills are promoted, which ultimately leads to better decisions and more efficient problem solving.
Another central element is the visualization of relevant key figures directly on the shop floor board. Important information such as production figures, quality indicators, machine availability and scrap rates are displayed there. These visualizations are updated regularly and give everyone involved a clear orientation about the production status and targets. A simple and clear presentation of the key figures is crucial in order to give employees an immediate overview and transparency.
Continuous improvement, also known as Kaizen, forms the basis of shop floor management. Employees' suggestions for improvement are collected, evaluated in a structured manner and implemented. Every step of progress is documented and visualized to make success visible. In addition, the team regularly - usually monthly or quarterly - reflects on progress and checks how shop floor management works overall and what further optimization potential exists.
In which areas can shop floor management be used?
Shop floor management is a versatile concept that originally comes from the production environment, but can be used successfully in many other areas. Shop floor management is also used in logistics and warehousing. Here it helps to coordinate work processes efficiently, keep an eye on inventory levels and ensure that goods are delivered on time.
Another important area of application is the maintenance and servicing of machines and systems. Here, shop floor management ensures structured monitoring and early error detection, which can optimize maintenance processes and increase the availability of the systems. Shop floor management can also be used in service and after sales service. Here it helps to shorten response times and increase service quality.
In the healthcare sector, shop floor management is used to optimize processes and improve cooperation between different departments. Teams can regularly exchange information about current challenges, which increases the quality of patient care through direct communication and rapid problem solving.
Another field of application is in construction and project management, where shop floor management helps to improve coordination between teams and trades. Regular on-site coordination and the visualization of project status and progress enable flexible adaptation to current challenges and thus promote the timely completion of projects.
Shop floor management is also becoming increasingly important in administrative and office areas. Shop floor management in the office focuses on the transparency of administrative processes with the aim of shortening lead times and optimizing team collaboration.
Goals of shop floor management:
Increase in efficiency
Direct communication and immediate problem solving on the shop floor enable production processes to be continuously optimized. This leads to increased productivity and efficient use of resources.
Increase in quality
Early detection and elimination of errors reduces waste and rework, which improves overall product quality. By closely monitoring the production processes, quality standards can be consistently maintained.
Quick response to problems
The regular presence of managers on the shop floor and the daily short meetings (shop floor meetings) enable problems to be quickly identified and resolved. This minimizes downtime and prevents small problems from becoming major disruptions.
Increasing employee motivation and commitment
The active participation of employees in decision-making processes strengthens their sense of responsibility and personal responsibility. Employees who can contribute their ideas and suggestions are generally more motivated and committed, which contributes to a positive working atmosphere.
Our products
-
5S Cleaning and Hygiene
Cleaning stations for production, workshops and officesThe apra-lean cleaning stations offer an...
-
5S Production / 5S Assembly
Process stations for production and assemblyThe apra-lean process stations are compact and...
-
Shopfloor Management and Workshop
The shop floor station is a mobile information board for use in...
-
First aid and Safety
Safety and a quick response option in the event of emergencies in...
-
Customised solutions
Wir entwickeln gemeinsam die perfekte Lösung für Ihre Anforderungen!