Efficient set-up of injection moulds
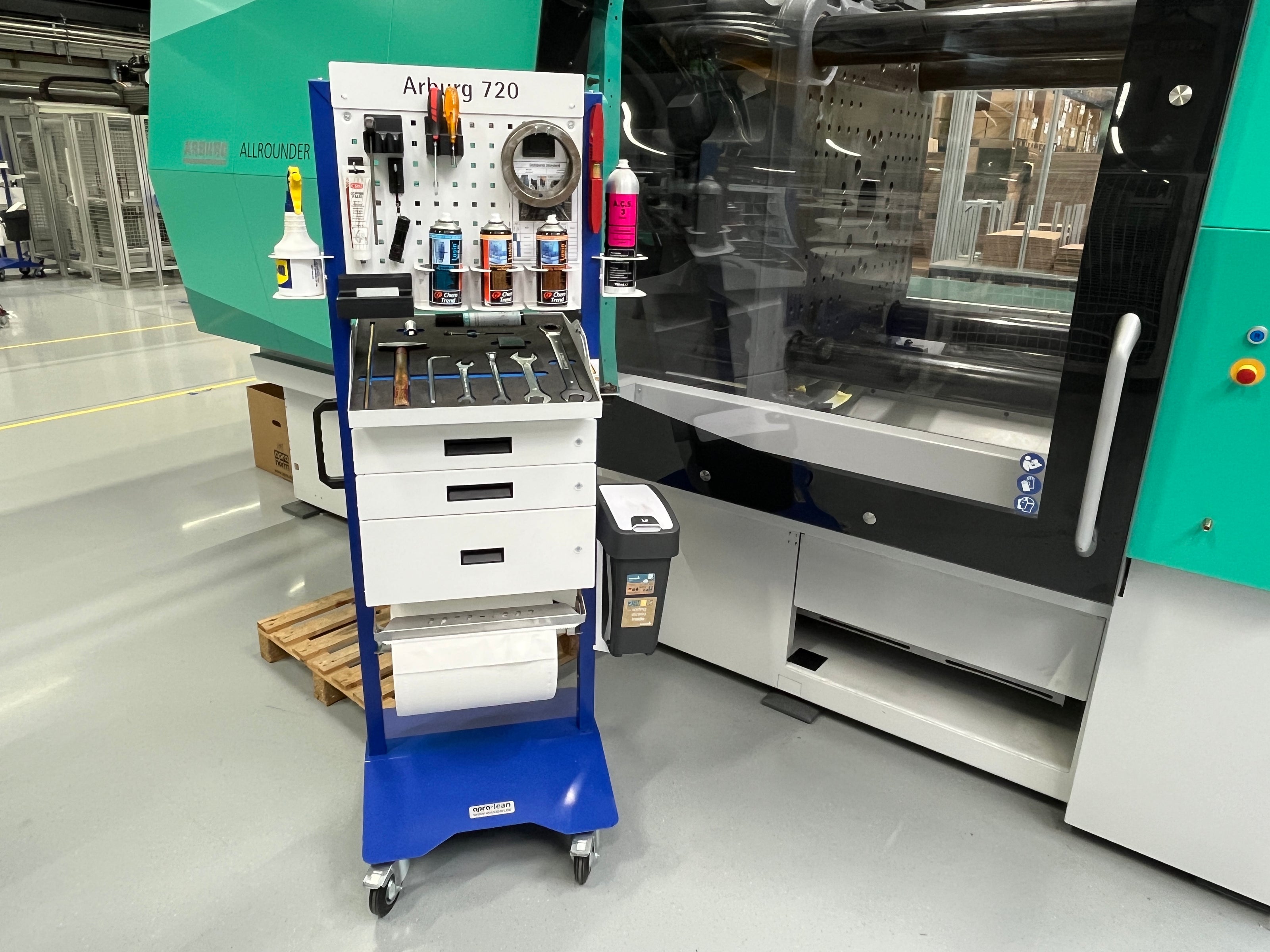
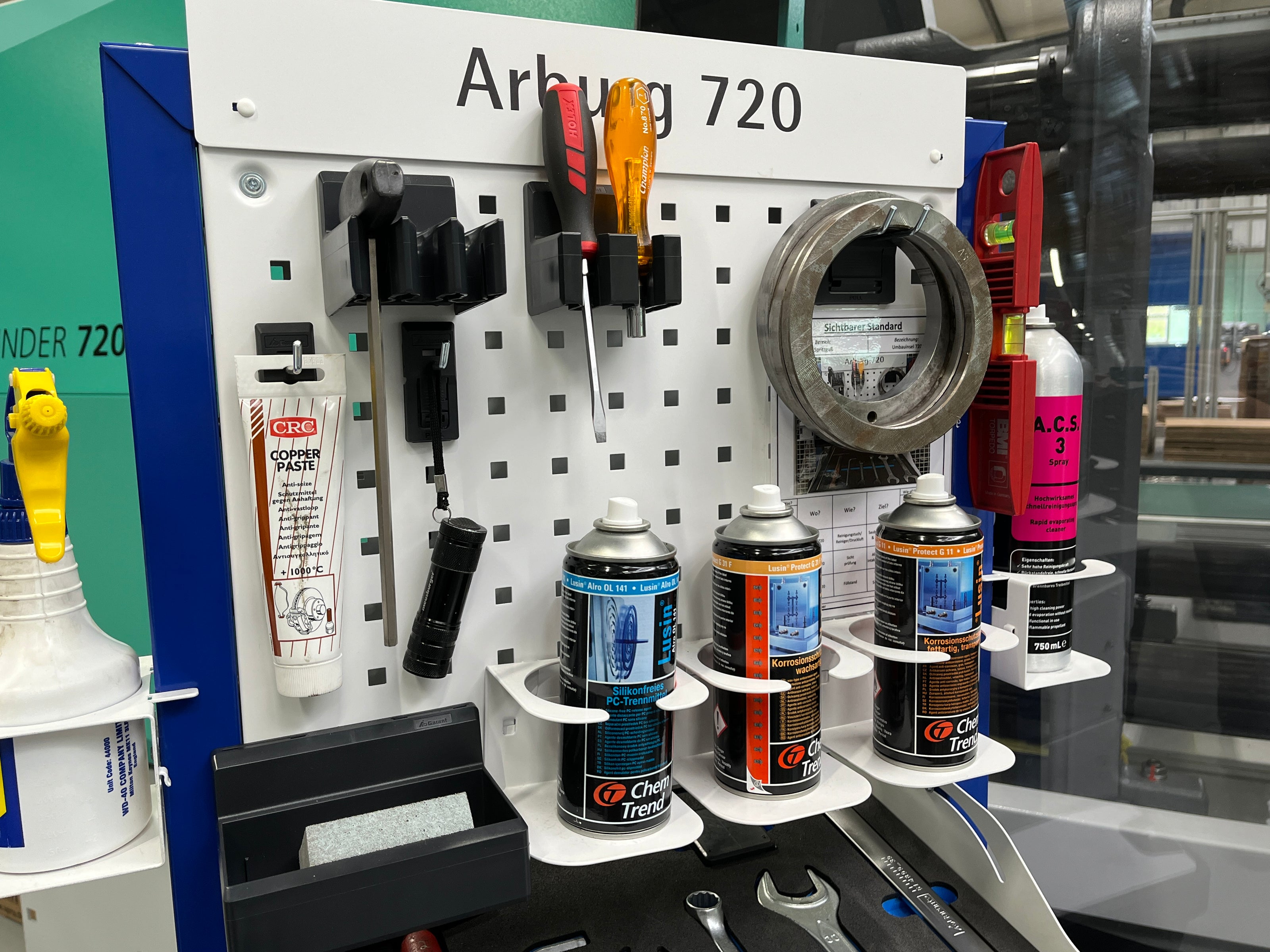

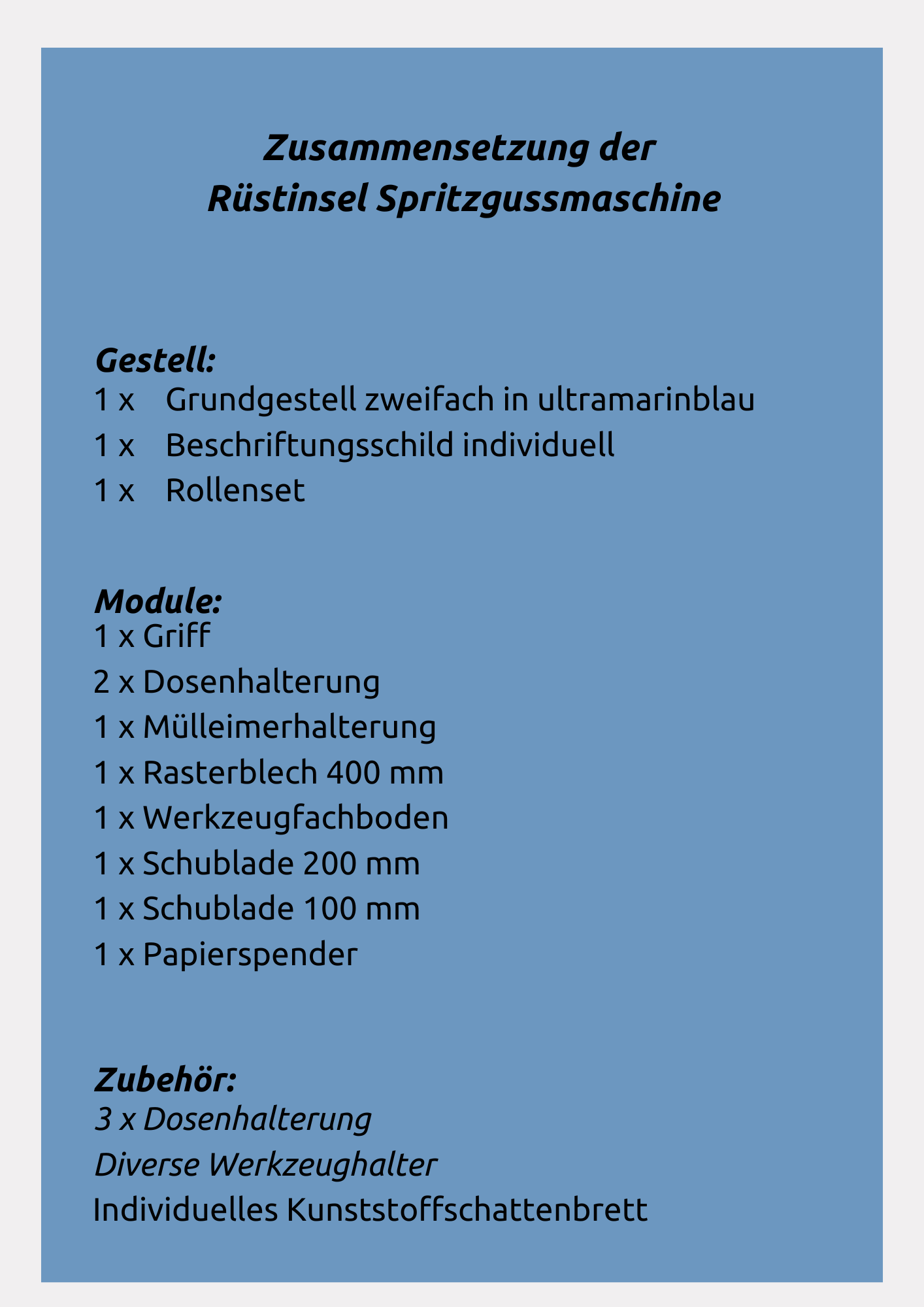
Long set-up times and disorganised work processes are a common problem in injection moulding production, causing not only efficiency losses but also unnecessary costs. In this article, we use a specific example to show you how targeted process optimisation using SMED analysis and the 5S method can achieve impressive results.
Get in contact with us:
The challenge: Minimising set-up times and search effort
Our customer's injection moulding production was faced with the following challenges:
- Long set-up times: Change processes took much longer than necessary.
- Unnecessary tool surplus: Too many or defective tools made it difficult to maintain an overview.
- High search effort: Tools were scattered in drawers and hard to find.
- No standards: Differently equipped tool trolleys and equipment led to inconsistent working methods.
These problems not only led to production delays, but also to frustration among employees.
The solution: a standardised rescue vehicle
By using the SMED-Analyse (Single-Minute Exchange of Die) and the 5S-Methodset-up has been systematically optimised:
- Analysis of the work process: First, the set-up times were analysed and all the tools required were identified.
- Eliminate the superfluous: Unnecessary or defective tools were consistently removed.
- Standardisierung: A standardised rescue vehicle was developed and equipped with all the relevant tools.
- Visual order: Each tool is clearly visible to eliminate search times.
The key to efficiency lay in a individual apra-lean set-up vehiclewhich has been specially adapted to the needs of employees.
The customer benefit: More efficiency in the setup process
The advantages of this optimization speak for themselves:
- Reduced setup times: All tools are within reach, which significantly accelerates the changeover processes.
- Standardized working method: Every employee can work efficiently with every setup cart, regardless of personal preferences.
- Clarity and overview: Through visual order, everything is immediately recognizable and ready for use.
- Faster handling: The ergonomics of the setup cart ensure intuitive use and faster processes.
Conclusion: Process optimization is worthwhile
Composition of the set-up terminal injection moulding
-
Basic frames
Regular price From €317,50 EURRegular priceUnit price / per -
Roller set
Regular price €79,65 EURRegular priceUnit price / per -
Handle module
Regular price €9,30 EURRegular priceUnit price / per -
Labeling sets Individual text
Regular price €79,65 EURRegular priceUnit price / per -
Drawers 2 x 100 mm
Regular price €252,50 EURRegular priceUnit price / per -
Drawer 200 mm
Regular price €190,00 EURRegular priceUnit price / per -
Paper dispenser
Regular price €50,90 EURRegular priceUnit price / per -
Grid plate 400 mm
Regular price €82,75 EURRegular priceUnit price / per -
Tool tray small
Regular price €63,70 EURRegular priceUnit price / per -
Trash can holder
Regular price €53,30 EURRegular priceUnit price / per -
Can / bottle holder
Regular price €25,30 EURRegular priceUnit price / per
1
/
of
11